Get Samples for Free!
Development History of Co-extruded Wood-Plastic Composite Materials in China
Wood-plastic composite (WPC) materials are eco-friendly composites made by processing wood fibers and plastics (such as polyethylene (PE) or polyvinyl chloride (PVC)). These materials combine the natural texture of wood with the durability of plastic. Due to their excellent physical properties and environmental benefits, WPC materials are widely used in interior and exterior decoration, landscaping, and architectural applications such as flooring, railings, wall panels, pergolas, and arbors. With technological advancements, co-extrusion technology has been introduced into the production of WPC materials, significantly improving their performance and expanding their application scenarios.
Co-extrusion is an advanced manufacturing process that optimizes the performance of WPC materials through a multi-layer structure design. In this process, traditional WPC material is typically used as the core layer, with a functional co-extruded surface layer applied on top. This surface layer enhances the material’s resistance to aging, weathering, and scratches while offering diverse visual effects, such as wood grain patterns and matte finishes. The application of co-extrusion technology plays a vital role in improving WPC material performance and promoting its commercialization.
The evolution of WPC materials has progressed from single-layer structures to multi-layer composite structures. Around 2007, the United States pioneered the application of co-extrusion technology in WPC production, marking a new chapter in the industry. By 2010, a lightweight core-shell structured functional WPC material production technology was disclosed, aiming to address some of the performance limitations of traditional WPC materials. These innovations laid the foundation for the development of WPC materials.
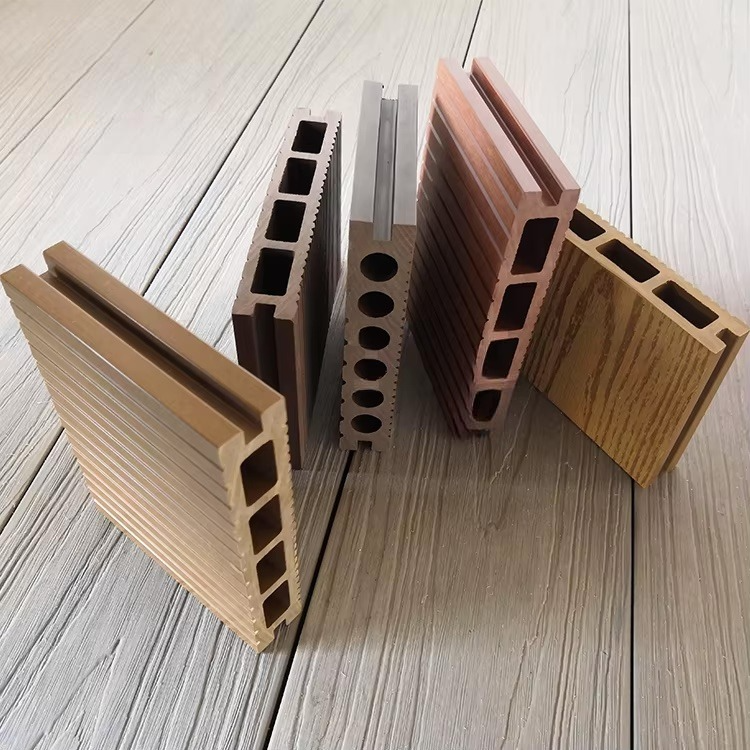
In 2012, a wood profile manufacturer developed a method to produce protective layers for co-extruded WPC profiles. By blending high-density polyethylene (HDPE) with ethylene acrylic acid copolymer (EAA), the bonding strength between the surface layer and the core layer was enhanced. Additionally, fillers such as nano zinc oxide were used to significantly improve weather resistance and scratch resistance. This method also provided a matte finish for the protective layer, further enhancing the product’s aesthetic and practical value. Meanwhile, other researchers also worked on developing new co-extruded profiles, gradually advancing the co-extrusion technology for WPC materials.
China’s research and application of co-extruded WPC materials started later but developed rapidly. Since 2010, domestic research institutions and companies have gradually introduced, absorbed, and innovated co-extrusion technologies, launching a series of co-extrusion products and techniques. For instance, domestic mold manufacturers designed unique mold flow channels and developed specialized molds to create realistic wood grain effects, supporting the diversification and customization of co-extruded WPC production. Continuous exploration and innovation by Chinese enterprises have led to the commercialization of co-extruded products, marking the initial stage of co-extruded WPC material development in China.
Currently, co-extruded WPC materials in China are in a period of rapid development. With further optimization of co-extrusion technology and improvements in the industrial chain, this field is expected to see even broader market potential. In the future, co-extruded WPC materials will continue to focus on environmental protection, performance, and aesthetic design, making significant contributions to the development of green building materials and the protection of the ecological environment.